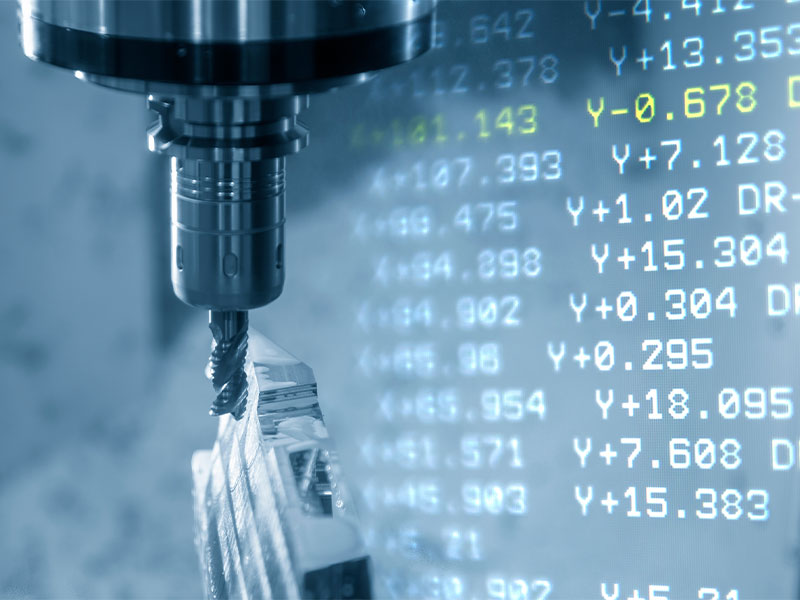
What are the Differences and When is One Better?
Like most manufacturing techniques, milling is an old and reliable method that has seen significant development over the past decades. Before the rise of computer numerical control (CNC), most manufacturers relied on conventional machines that they hand-operated in order to shape various materials into usable parts. However, as computers grew more sophisticated, CNC mills quickly took the manufacturing industry by storm in the latter half of the twentieth century. Thanks to the exponential growth of technology, it quickly developed into the much more complex five-axis technology in use by many manufacturers today.
Despite the significant changes that this type of manufacturing has undergone, each method–conventional, CNC, and five-axis milling–still proves to have something to offer depending on the project and the circumstances.
Traditional or Conventional Milling
Traditional milling has its roots in one of the oldest machining processes in the world, though until the integration of computer numerical control, milling machines were operated by hand. The manufacturer would clamp the workpiece into place and then carefully guide the tool along it, whether it was a drill, blade, or other tool.
Though not nearly as accurate or efficient as the computerized versions, traditional milling still has plenty of applications in the modern day. It can be used for roughing or working with large workpieces that a typical CNC machine can’t accommodate. Some manufacturers offer traditional milling services for short run projects or specialized needs that require that hands-on expertise that computerized machines can’t always offer.
CNC Milling
Computer numerical control or CNC led to a massive shift in manufacturing. Now, directions for the cutting tools could be programmed into the machine, and required little to no operator oversight besides adjusting the workpiece and tooling between operations. Thanks to CNC, milling operations also became far more efficient, shortening cycle times and improving consistency across part batches.
CNC Milling is used throughout manufacturing thanks to these benefits, and can be used for low to high volume production in a wide range of industries–aerospace, electronics, medical equipment manufacturing, military equipment, automotive–and that’s just scratching the surface. It offers high precision and consistent quality even in high volume, long-run production, and offers a quick and easy method for rapid prototyping.
Five-Axis Milling
Five-axis CNC milling is one of the more recent developments in milling technology, offering manufacturers a much more flexible and versatile way to make parts for their customers. Most CNC mills have a tool that can cut along three axes–X, Y, and Z–which limits them when it comes to making unconventional shapes, deep cavities, or other complicated features. Five-axis mills also work on those same axes, as well as the A and B axes, which allow the tool to rotate around the workpiece and operate on it from all directions.
Five-axis mills decrease and in some cases even eliminate the need for downtime between different operations that typical CNC mills require to readjust the workpiece and the tools. This helps to shorten lead times and reduces the chances of human error throughout production. They’re excellent choices for all of the parts that normal CNC milling machines can’t easily accommodate, such as parts with complicated geometries, large or difficult features, smooth and contoured edges, and more.
Final Thoughts
Regardless of the type of CNC milling, this is one type of CNC machining service that shows the history of manufacturing methods over the past century, and how valuable each improvement has been, and still is today, in modern industry. While traditional CNC mills and five-axis mills have become the go-to method, there are still plenty of uses for conventional milling as well. What CNC machining service you choose ultimately depends on the requirements of your project.
About Trimen Industrial, LLC
Established in 1993, Trimen Industrial is an ITAR registered and ISO 9001 certified manufacturer, offering just about every type of CNC machining service that you could need. If you’re interested in our services, head over to our website to contact us for more information.